A well-run warehouse is a thing of beauty. Boxes move swiftly from one stage of the shipping process to the next, workers zip around on forklifts, and customers get their orders quickly and efficiently. A well-run warehouse keeps costs down and ensures that orders are filled promptly and accurately. However, achieving this level of efficiency is no easy feat.
There are a lot of moving parts in a warehouse, and if just one component isn’t working properly, it can throw the whole operation off balance. Here, we explore some of the ways you can keep your warehouse workflow running smoothly. By implementing these best practices, you can ensure that your warehouse is running at peak efficiency and your customers are getting their orders on time.
1. Conduct a Warehouse Audit
Before you can start implementing changes in your warehouse, you need to take a step back and assess what’s actually going on. A warehouse audit is a review of your current operations, procedures, systems, compliances, and regulations. It’s an opportunity to identify areas that are working well and update your regulations. You can do that by consulting IMDG books and IATA books, for instance. Conducting a warehouse audit can be a daunting task, but here are a few tips:
- Define your goals: Do you want to improve safety, efficiency, or both? Keep your goals in mind as you conduct your audit.
- Gather data: Collect data on every aspect of your operation, from how many orders you ship each day to how often accidents occur. This will help you identify areas that need improvement.
- Evaluate your findings: Are there any glaring problems? Are there any areas that stand out as needing attention? Make a list of all the issues that need your attention.
2. Practice Lean Warehousing
Just as lean manufacturing cuts waste and improve efficiency in the production process, lean warehousing does the same for storage and distribution. By eliminating waste and streamlining operations, lean warehousing can help to improve profitability and competitiveness.
The first step involves identifying areas of waste. This might include things like excessive inventory levels, incorrect orders, and damaged goods. Once you’re done identifying these areas, implement changes that will eliminate them. This might involve streamlining receiving and shipping operations, reducing error rates, or increasing the accuracy of inventory data.
3. Invest in Quality Training Processes for Your Employees
Your employees are the backbone of your operation, and they need to be knowledgeable and efficient to keep things running smoothly. Warehouse work can be grueling. They’re on their feet all day, moving around heavy boxes and dealing with dangerous machinery. It’s no wonder that many accidents happen in warehouses every year.
However, by training your employees on how to properly operate forklifts, handle hazardous materials and use warehouse equipment such as pallet racks, you can help create a safer working environment. Proper training can even improve job satisfaction and productivity.
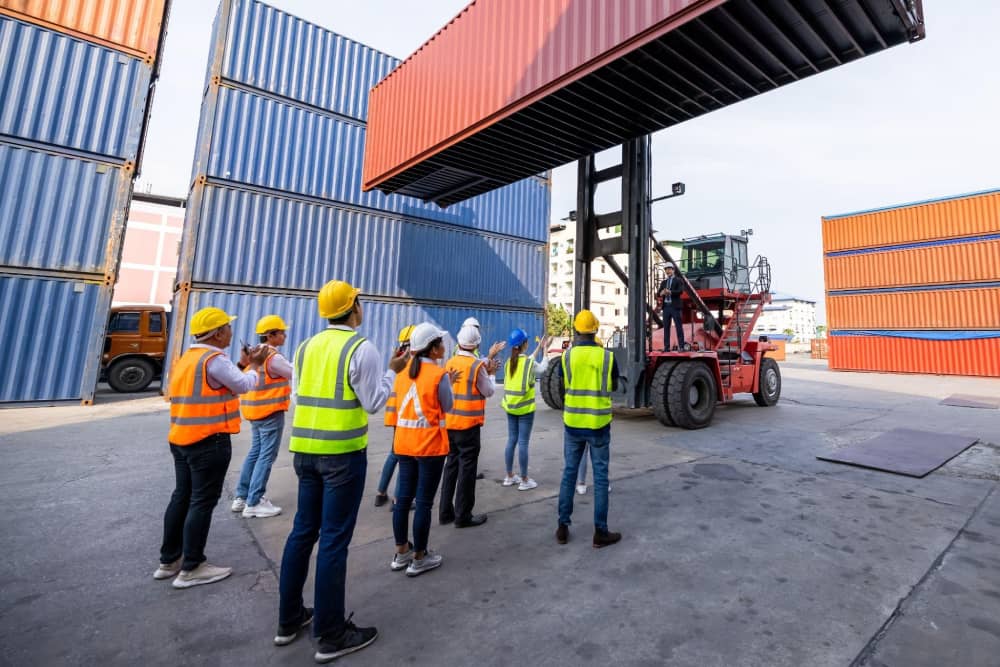
4. Use Proper Labeling for All Products
In a warehouse, labels are key. They help you keep track of inventory, find items quickly and keep your shelves organized. But not all labels are created equal. For maximum efficiency, it’s important to use the right label for each job.
Barcodes, for instance, are a must for tracking inventory. By scanning items with a barcode reader, you can quickly and easily keep track of what’s in stock. You can also use barcodes to automatically update your inventory records when items are sold or shipped.
RFID tags are similar to barcodes, but better because you can read them without being in the line of sight. That means you don’t have to scan each individual item. You can just walk through the warehouse with an RFID reader, and it’ll automatically update your inventory records. RFID tags are more expensive than barcodes, but they can be a real-time-saver in a large warehouse.
Printed labels are also perfect for quickly finding items on shelves. They can be printed with text, images or even QR codes so that you can quickly look up more information about an item. Adhesive labels are ideal for attaching to containers or other surfaces. They’re great for temporary labeling—for example, if you need to label a box for shipping but don’t want to write directly on the box.
5. Maximize and Optimize All Available Space
Maximizing the use of vertical space is a great way to get the most out of your warehouse without having to expand the footprint. Adding mezzanines or shelves can double or even triple the amount of inventory you can store in the same amount of space. And if you’re really looking to optimize your warehouse, consider installing an automated storage and retrieval system (AS/RS).
AS/RS systems are computer-controlled, and they typically use conveyors and cranes to move items around. The items are stored in specific locations, and the system keeps track of them, so they can be retrieved quickly when needed. This type of system works well for storing just about anything, but it’s particularly well-suited for handling heavy or large items.
6. Choose the Right Containers for Your Warehouse
When it comes to storage, it’s important to choose the right containers for your warehouse based on the type of product you’re storing and the amount of space you have available. For example, if you’re storing perishable goods, you’ll need a refrigerated container to keep them fresh.
If you’re short on space, consider using stackable containers. If you’re storing high-value items, security is a must, so be sure to choose lockable containers.
7. Leverage Automation and Digitization
In the age of automation and digitization, there are more opportunities than ever to leverage technology to streamline warehouse operations. One way to do this is to invest in a warehouse management system (WMS).
A WMS can provide real-time visibility into inventory levels and locations, as well as track inbound and outbound shipments. You can use this information to optimize stock levels and reduce the need for manual counting and picking. Additionally, automated packaging and labeling systems can help to improve accuracy and reduce labor costs.
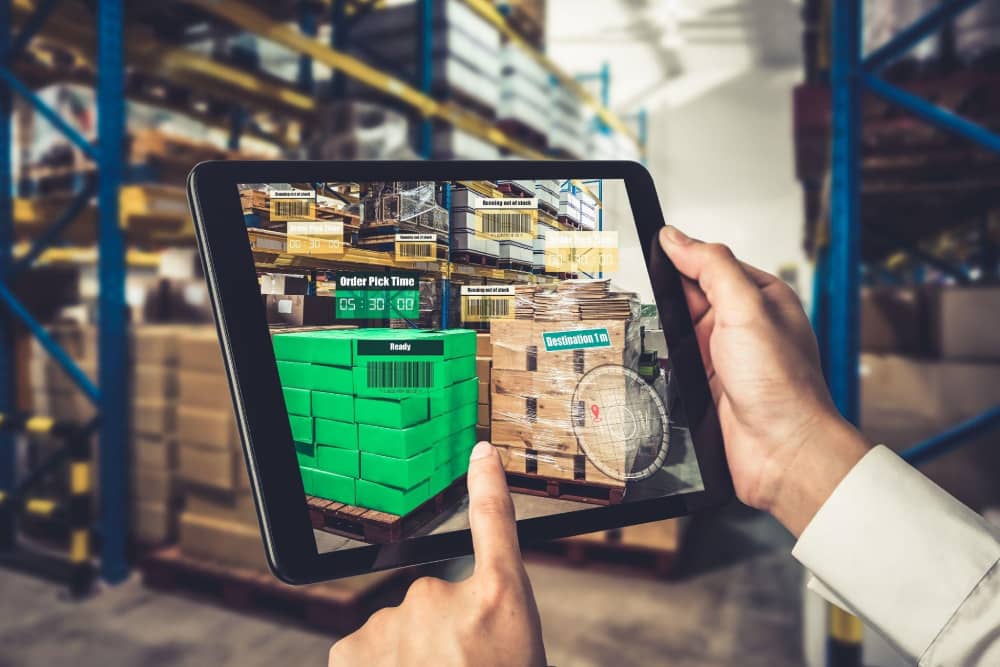
Boosting Warehouse Efficiency
Implementing these strategies will help to optimize your warehouse and improve efficiency. By maximizing space, leveraging automation, and choosing the right containers, you can ensure that your warehouse is running smoothly and efficiently.